Copper vs. Aluminum Stabilizers: Which is Better?
When choosing a voltage stabilizer, one of the key considerations is the material used for the windings—typically copper or aluminum. Both materials have their advantages and disadvantages, so it’s important to understand their differences to make an informed choice for your electrical equipment.
Copper Stabilizers: The Premium Choice
Copper is known for its superior conductivity, meaning it transmits electricity more efficiently, with less power loss. This results in better overall performance and energy efficiency. Copper also has high durability, being resistant to corrosion and oxidation, ensuring a longer lifespan for the stabilizer. Additionally, copper can handle higher currents and dissipate heat more effectively, making it ideal for protecting heavy-duty appliances like air conditioners and industrial machinery.
Aluminum Stabilizers: The Budget-FriendlyOption
Aluminum, on the other hand, is lighter and cheaper than copper, making it an attractive option for budget-conscious buyers. However, it has lower electrical conductivity, meaning it requires thicker wires to carry the same current as copper, which can lead to bulkier stabilizers. Aluminum is also more prone to oxidation, which can affect the efficiency of the stabilizer over time.
The Verdict: Copper Wins for Performance, Aluminum for Cost
While copper stabilizers offer better efficiency, durability, and heat dissipation,they come at a higher price. If you’re looking for long-term reliability and higher performance, especially for sensitive or high-power equipment, copper is the way to go. However, if you’re on a budget and need a stabilizer for less demanding applications, aluminum stabilizers can still provide adequate protection.
In the end, the choice between copper and aluminum stabilizers comes down to your specific needs and budget.
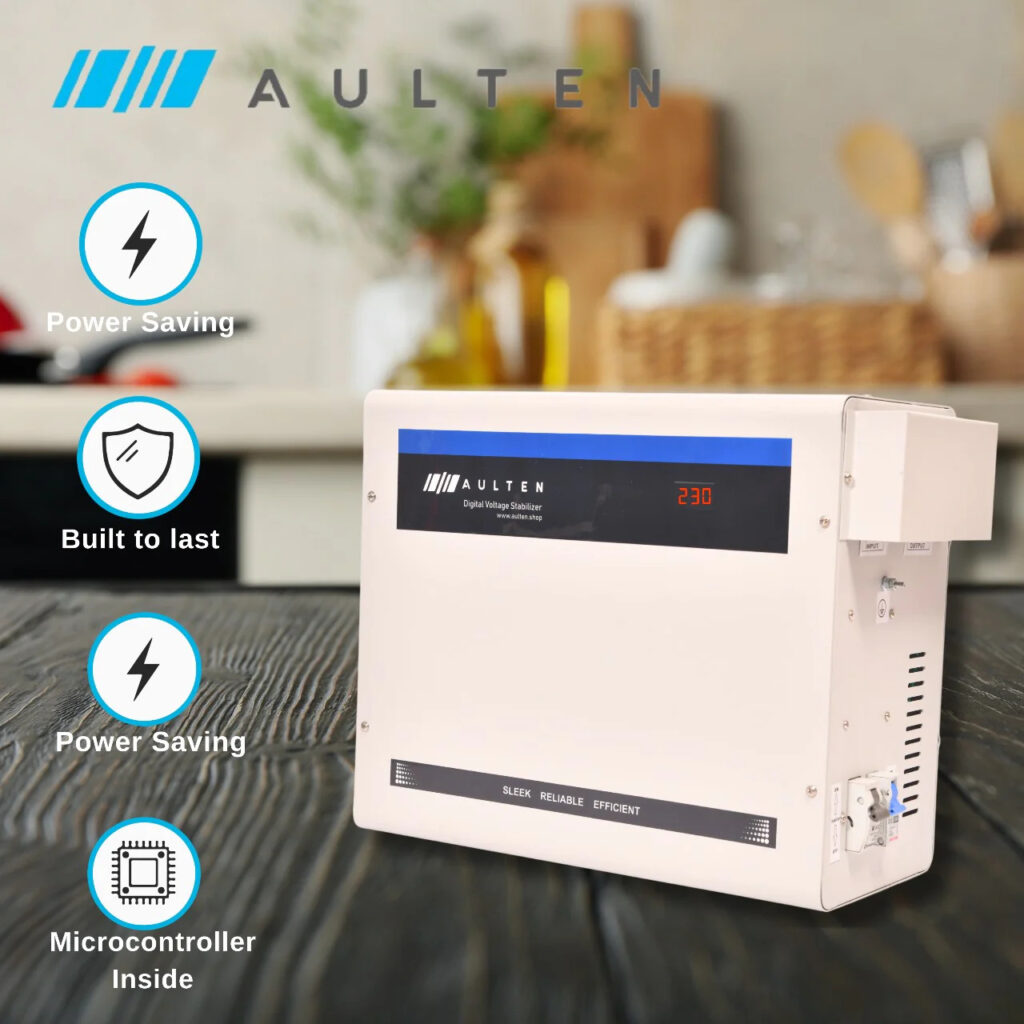
This post was created with our nice and easy submission form. Create your post!